How to make a sealing gasket with CNC cutting machine? Today, we’ll show you how a new user made a gasket with an oscillating knife cutter.
Suppose, you have just received an AMOR CNC gasket cutting machine, have completed the basic installation work, completed the platform inspection work on the machine, and have also completed the software installation and data reading work on the computer. Are you wondering how to install a CNC knife cutting machine? Don’t worry, friends, we’ll explain it in detail in the next article – how to install a CNC oscillating knife cutter, now let’s move on to how to make a gasket with an oscillating knife cutter.
First, we choose the sealing material to be cut – 3mm non-asbestos sheet, and place it on the working platform of the machine. Since the machine model we use is AMOR1625MK CNC gasket cutting machine, the effective working size is 1600mmX2500mm, and the size of the processing material is only 500mmX500mm. In order to ensure that the material is firmly fixed on the working platform, we need to activate the partition adsorption function, which can enhance the ability of vacuum adsorption, and adsorbs specifically for the area where the material is located.
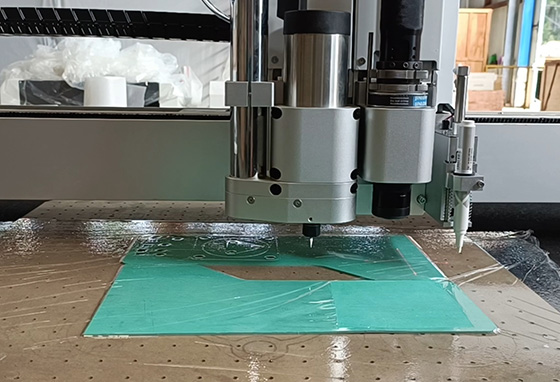
Make Custom Gaskets with AMOR CNC Cutting Machine
The second step is to draw the graphics to be processed in the CAD software. Of course, we can also look for the graphics to be cut in the professional gasket nesting software, because it comes with more than 100 kinds of commonly used gasket graphics without CAD work. Just enter the data to get the processing graphics. Then, we only need to enter the size of the material to be processed and the number of cuts in the software, and the software will automatically nest according to these data. In just 1 minute, we can get the best nesting scheme. Save nesting time, improve material utilization, and realize intelligent processing.

professional gasket nesting software
When we have selected the processing materials and finished drawing the processing graphics, you must be thinking that the next step should be cutting, right?
No, before cutting, we also need to select the appropriate blade and tool for the material and graphics to be processed.
We take 3mm non-asbestos plate as an example, we recommend using 400W high-power electric oscillating knife or high-power pneumatic oscillating cutting tool, because 400W electric oscillating cutting tool does not need 0.6MPA compressed air, so its processing cost can save 11KW per hour power. Therefore, we recommend the use of 400W electric oscillating tools.

400W electric oscillating tools
If the diameter of the small circle we cut is less than 10mm, then we recommend choosing a professional small circle cutting knife, because its blade adopts a vertical design, and the blade tip adopts an obtuse angle design. When cutting materials with high hardness, the blade tip is not easy to be damaged, When cutting small circles, there is no corner overcut, which can achieve the best cutting effect, especially suitable for high-density asbestos board and rubber board cutting.

small circle cutting knife
After we have installed the selected knives and blades on the machine, we have to complete a very important setting, which is to set the depth of cut and knife width compensation. The setting of this step is done on the control panel of the machine. Only by setting the correct tool depth and tool compensation data can we obtain a good cutting effect. About its setting method, we will write an article to explain it. If you are interested, you can bookmark our website. We will continue to update our professional knowledge about the vibrating knife-cutting machine.
When we have completed all the above settings, we can proceed to the third step to make the sealing gasket.
In the third step, we open the processing graphics in the control software of the machine and optimize the processing graphics before processing.
First, we set the correct pen number for the processing graphics. At this time, we want to use an oscillating knife to cut the material, then we set the pen number of the graphics to SP4;
Then, we need to set the best cutting starting point – the middle position of the straight line;
Then, we perform overlapping and closing checks on the graphics to obtain the best cutting data;
Finally, we need to sort the graphics, the best cutting order – cut small graphics first, then large graphics; first cut the graphics in the center of the material, and then cut the graphics near the edge of the material.
Do you feel that these optimizations are very complicated? In fact, we only need to save these optimization data in the configuration options of the software, and then just click the “Optimize Configuration” command to complete all optimizations with one click.

optimize the processing graphics before processing
When these optimizations are done, we can send the graph to the machine.
Since we have completed the various settings of the machine before, so now we only need to set the processing speed for the material on the operation panel.
So how to set the processing speed?
We can set the linear speed, curve speed, small circle speed, and tool falling speed of vibrating knife cutting in the speed interface of the operation panel. A principle can be followed when we set these speeds – the harder the material, the lower the speed. Taking 3mm non-asbestos board material as an example, we set the linear cutting speed to 100mm/s, the curve speed to 60mm/s, the small circle speed to 30mm/s, and the tool falling speed to 100mm/s.

how to set the processing speed
Finally, we need to set the starting point of processing – move the red laser positioning system to the starting point of the material, and click “Set Zero” on the panel, and we have completed the starting point setting. If you want to check the processing range, just click the “【】” button on the operation panel to check whether the processing range exceeds the material.

et the starting point of processing
When everything is completed, we can click “Start”, and the machine will start to cut automatically. Now, let’s take a look at the processing process of the machine.